فولاد خام یک آلیاژ آهن و کربن است که از منابع طبیعی فراوان و از مواد بازیافت شده تولید میشود که حاوی ۹۹.۲ درصد آهن است. مهمترین ماده اولیه برای تولید فولاد، سنگ آهن است که در زنجیره تولید، با فرآیند ذوب و احیا آهن از آن جدا میشود. سنگ آهن پس از تبدیل به کنسانتره و سپس گندله و در نهایت به فولاد تبدیل میشود.
فولاد پس از نفت خام دومین ماده پر مصرف در کشورهای مختلف جهان بوده و کاربردهای بیشمار آن در صنایع مختلف غیرقابل انکار است. صنایعی نظیر ساختمان و انبوهسازی، خودروسازی، تولید قطعات، لوازم خانگی و … از فولاد به عنوان مواد اولیه خود استفاده میکنند.
در سالهای اخیر رشد مصرف فولاد در کشورهای مختلف به شدت در رشد اقتصادی آنها موثر بوده است. تا جایی که گفته میشود هر ۱% رشد مصرف فولاد در یک کشور، معادل رشد اقتصادی ۰.۸۵% آن کشور باشد. صنعت فولاد ایران به خاطر نقش مهم فولاد در توسعه صنعتی و رشد اقتصادی کشورها، از اولویت بالایی در برنامههای توسعهای کشور برخوردار است. فولاد مفیدترین، ارزانترین و پراستفادهترین فلز و نیز مهمترین محصول ساختمانی و مهندسی در جهان است. به همین دلیل صنعت فولاد نیز طرفداران زیادی در بازار سرمایه دارد.
سنگ آهن دومین کالای مهم پس از نفت است که بزرگترین معادن آن در استرالیا و برزیل قرار گرفتهاند. سنگ آهن ماده اصلی تولید فولاد است و حدود ۹۸ درصد از سنگ آهن استخراجی برای تولید فولاد استفاده میشود.صنعت فولاد در بسیاری از کشورها صنعت اول شناخته میشود تا جایی که تولید و مصرف فولاد امروز، یکی از شاخصهای اصلی توسعه یافتگی به شمار میآید. حضور صنعت فولاد در یک منطقه بر فرآیند توسعه فرهنگ، سطح دانش، اشتغالزایی، پژوهش و تجارت آن منطقه تأثیر به سزایی دارد.
بررسی چرخه تولید فولاد
طبیعتا از اولین اقدامات در زنجیرهی تولیدی محصولات فولادی اکتشاف معادن سنگآهن است. پس از اکتشاف معادن مسئلهای که بسیار بااهمیت است سنجش توجیهپذیری اقتصادی برداشت از معادن است. در چنین مرحلهای میبایست عیار خاک معادن ارزیابی شود تا در صورت داشتن حد نصاب لازم بهرهبرداری از آن آغاز شود. سنگآهن، نوعی سنگ معدنی است که حاوی رگههایی از آهن است و اولین حلقه از فرایند تولیدی فولاد با ذوب و احیای سنگآهن آغاز میشود. در فرایند برداشت این مادهی معدنی قطعا باطلههایی نیز به وجود خواهد آمد که این موضوع امری اجتنابناپذیر است اما شرکتها باید سعی کنند تا هزینههایی را برای برداشت همین باطلهها از معدن در نظر بگیرند چراکه در صورت غفلت به یکباره مجبور بهصرف هزینههای سنگینی در این خصوص به علت انباشت باطلهها خواهند شد. بهطورکلی سنگآهن به دو گونهی مختلف سنگآهن دانه بلند و کنسانتره وجود دارد. هر یک از این انواع سنگآهن جهت استفاده در یکی از روشهای فراوری مورداستفاده قرار خواهند گرفت. اولین نوع از سنگآهن، سنگآهن دانه بلند است که از آن در روش فراوری کوره بلند استفاده میشود. در بخش بعدی در خصوص روش کوره بلند توضیحات بیشتری ارائه خواهیم داد.
نوع دیگری از سنگآهن که مورد استفاده قرار میگیرد در واقع همان سنگآهن با عیار پایین یا کلوخه است. این نوع از سنگآهن برای روش فراوری احیای مستقیم که در ادامه به توضیح بیشتر در خصوص آن خواهیم پرداخت. در سطح جهان، سنگآهنی که معاملات با آن انجام شده و بهنوعی لیدر بازار سنگآهن در جهان محسوب شده و معاملات مختلف خود را با آن وفق میدهند، سنگآهن عیار ۶۲ درصد چین است. از آنجایی که چین بیشترین تقاضا را برای سنگآهن در جهان دارد، شاخص معیار سنگآهن نشاتگرفته از آن است.
کنسانتره چیست؟
پس از استخراج و انتقال مواد معدنی به واحدهای صنعتی، در کارخانهها، مواد معدنی را به کنسانتره تبدیل میکنند. کنسانتره سنگآهنی است که پر عیار شده است. اصطلاح کنسانتره در تمامی فلزات معدنی موضوعیت دارد و کنسانتره مس، کنسانتره سرب و امثال آن نیز وجود دارد. کنسانترهها که از سنگآهن به دست میآیند طبیعتا دارای ضریب تبدیل است اما این ضریب تبدیل ثابت نیست و بنا به جنس سنگآهن و عیار خاک معدنی و عیار کنسانتره تولیدی متفاوت خواهد بود. هدفگذاری عیار در کنسانتره چیزی در حدود ۶۷ الی ۶۸ درصد است.
گندله چیست؟
یکی دیگر از اصطلاحات موجود در زمینهی تحلیل صنعت فولاد گندله است. گندله در واقع همان کنسانتره است با این تفاوت که گرانوله شده است و به شکل گلوله درآمده است. بنابراین ضریب تبدیل کنسانتره به گندله یکبهیک است. گندله مادهای است که برای تولید آهن خام و در نهایت استحصال فولاد در هر دو روش احیای مستقیم (قوس الکتریک) و کوره بلند کاربرد دارد.
معرفی آهن اسفنجی
آهن اسفنجی تفاوت ظاهری با گندله ندارد و قدری رنگ آن متفاوت است اما از نظر فرایندی یک مرحله بعد از گندله است. در فرایند تولید فولاد میتوان گفت در واقع این آهن اسفنجی است که به فولاد تبدیل میشود. در روش احیای مستقیم (که در بخش بعد به طور مفصل به آن خواهیم پرداخت) گندله را با بهرهگیری از گاز طبیعی به آهن اسفنجی تبدیل میکنند. ضریب تبدیل این تغییر برابر با ۱٫۴۶ است و این بدان معناست که برای استحصال ۱ تن آهن اسفنجی میزان گندلهی لازم برابر با ۱٫۴۶ تن خواهد بود. عیار آهن اسفنجی به فولاد نزدیکتر شده است اما ظاهر آن مشابه گندله است. هر چه عناصر مازاد و کربن کاهش پیدا کند، فولاد خالصتر و بهتری نیز تولید خواهد شد.
معرفی فولاد نیمه ساخته
فولاد نیمهساخته مرحلهی پس از آهن اسفنجی است. در این مرحله که تقریبا وارد فاز ریختهگری نیز شده است، متناسب با مصارف و تقاضایی که نسبت به فولاد وجود دارد، محصول فولاد به دستآمده را به اشکال مختلفی تبدیل میکنند. بهعنوان انواع مختلفی از فولاد نیمهساخته میتوان به شمش، بیلت، بلوم و اسلب اشاره کرد که متناسب با هر محصولی، یکی از این انواع تولید میشود. به طور مثال اسلب برای تولید ورقهای فولادی کاربرد دارد. معیار تقسیمبندی این محصولات نیز صرفا ابعاد شکل ظاهری آنها است.
ورق فولادی چیست؟
ورقهای فولادی مصارف بسیار متنوعی داشته و در صنایع پرشماری کاربرد دارند. از جملهی این صنایع میتوان به خودروسازی، لوازمخانگی، ساختمانی و غیره نیز اشاره کرد. ورقها نیز انواع و مراحل مختلفی دارند. اولین مرحله پس از اسلب ورق گرم است، ورق گرم تولیدی ممکن است به ورق سرد تبدیل شود و یا اینکه به شکل ورق گالوانیزه (قلع اندود) یا ورق پوششدار تبدیل شود. از ورق گالوانیزه در صنایعی نظیر خودروسازی استفاده میشود. برای گالوانیزه کردن نیاز به فلز روی است و بخش زیادی از تقاضای روی در دنیا برای گالوانیزه کردن است. بنابراین رشد قیمتی و رشد تقاضای ورق گالوانیزه سبب رشد تقاضای فلز روی و افزایش قیمت آن میشود. بهاینترتیب با افزایش قیمت ورق گالوانیزه حاشیه سود روی نیز افزایش خواهد یافت.
به طور کلی فولاد به دو روش کوره بلند و احیا مستقیم تولید میشود که در ادامه به بررسی این دو روش میپردازیم:
معرفی انواع روشهای فرآوری سنگ آهن
روش کوره بلند
اولین روش فراوری سنگآهن جهت تبدیل آن به محصولات لازم در صنعت فولاد، روش کوره بلند است. برای استفاده از روش کوره بلند برای فراوری سنگآهن میبایست از سنگآهن دانهبندی شده استفاده شود. در ایران این روش چندان رایج نیست و بیشتر سنگآهن دانهبندی شده نیز صادر میشود. همچنین در این روش بهرهگیری از زغالسنگ اهمیت بالایی دارد و کشور چین به دلیل در اختیار داشتن منابع لازم در این زمینه، عمدتا از این روش استفاده میکند. در این روش معادل نیمی از فولادی که قصد تولید آن را داریم، کک زغالسنگ به کوره افزوده میشود. طبیعتا یکی از مواردی که بر فرایند سودآوری شرکتها تأثیرات مستقیمی را خواهد داشت تفاوت در روش فراوری آنها در سنگآهن است. به طور مثال یکی از دلایل عمدهای که سبب شده تا همواره سودآوری کارخانهای نظیر ذوبآهن اصفهان نسبت به فولاد خوزستان کمتر باشد تفاوت در روش فراوری سنگآهن در آنها است. در ایران گاز صنایع یکی از کمترین قیمتها را در سطح جهان دارد و به همین علت صنایعی که از روش احیای مستقیم که در ادامه به آن خواهیم پرداخت، استفاده میکنند به دلیل بهرهگیری از گاز در فرایند فراوریشان، توانایی محقق کردن سود بیشتری دارند.
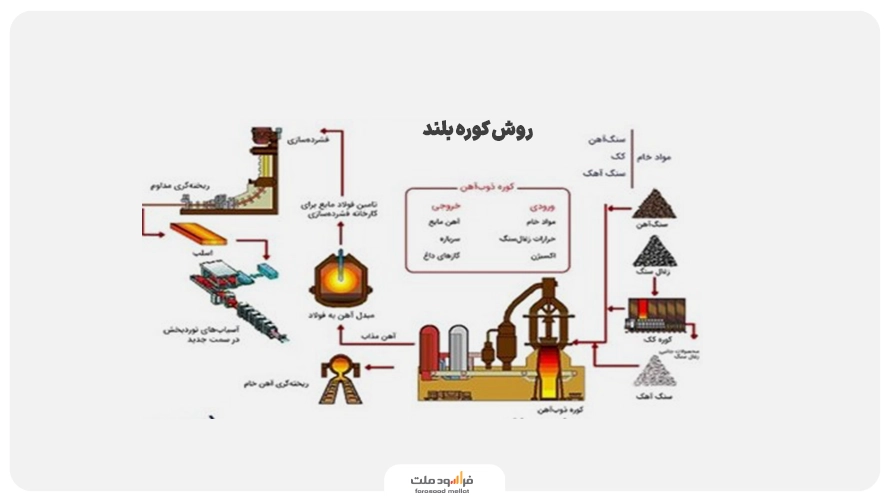
روش احیای مستقیم
این روش در کارخانههای ایران رایجتر بوده و عمدهی کارخانههای فولاد در ایران از این روش استفاده میکنند. روش احیای مستقیم از دو بخش تولید آهن اسفنجی و سپس ذوب آن در کورههای الکتریکی و با استفاده از جریان بسیار قوی برق تشکیل میشود. در این روش ذرات اکسیدی آهن (سنگ آهن) در تماس با گازهای احیاکننده مثل هیدروژن و مونواکسید کربن در دمای ۷۵۰ تا ۹۰۰ درجه سانتیگراد احیا شده و به آهن اسفنجی تبدیل میشوند. سپس آهن اسفنجی به دست آمده در کورههای الکتریکی بسیار بزرگی قرار گرفته و با استفاده از جریان بالای برق فرآیند ذوب و فولادسازی صورت میگیرد. از مزایای استفاده از این روش نسبت به کوره بلند عدم نیاز به ذغال سنگ (کُک) به عنوان منبع حرارت و استفاده از جریان برق، کاهش آلودگیهای زیستمحیطی و عدم نیاز به مواد اولیه فرآوری شده (مثل گندله) را میتوان نام برد. نهایتا پس از طی مراحل فوق و با استفاده از یکی از روشهای کوره بلند یا احیای مستقیم، سنگآهن استخراج شده از معادن تبدیل به شمش فولاد خام شده و برای تولید محصولات بعدی آماده میشود.
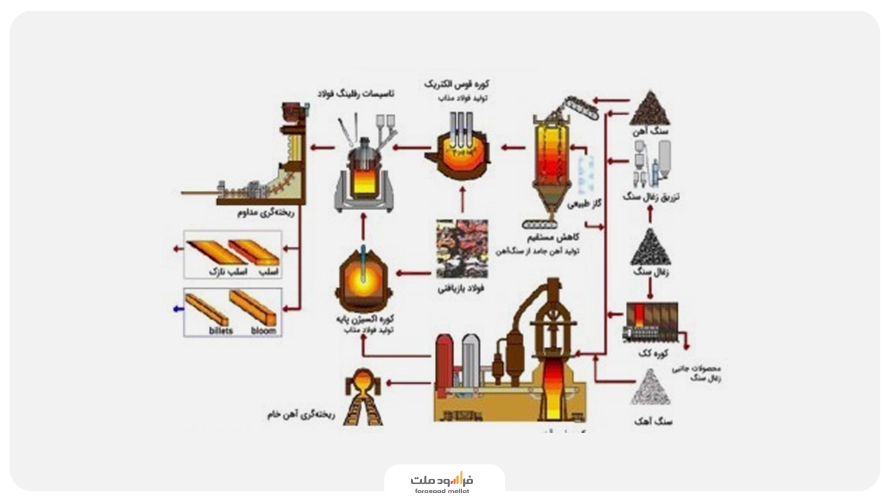
ساختار هزینه تولید فولاد
عمده هزینه برای تولید فولاد، مواد اولیه آن شامل سنگ آهن، زغال سنگ، سنگ آهک و آهن قراضه میباشد که چیزی حدود ۷۰ درصد از هزینه تولید فولاد است. بعد از مواد اولیه، هزینه سربار تولید شامل هزینه های حمل و نقل، تبلیغات، استهلاک، حقوق و دستمزد و سایر هزینه ها میباشد که چیزی در حدود ۲۲ درصد از بهای تمام شده را به خود اختصاص میدهد. در نهایت انرژی به کار برده شده در ساخت فولاد به عنوان یکی از مهمترین هزینهها در ساخت فولاد شناخته میشود. انرژی بخش عمده ای از ھزینهھای تولید فولاد را به خود اختصاص داده است، در نتیجه بھینه سازی مصرف انرژی، کاھش ھزینهھای تولید و در نھایت افزایش میزان رقابت پذیری این صنعت را به دنبال خواھد داشت. میزان بھره وری انرژی در تاسیسات ساخت فولاد با توجه به عواملی چون روش تولید، نوع آھن خام و کک مصرفی، تنوع محصولات تولیدی و تکنولوژی کنترل ماشین آلات بسیار متغیر است. در فرایند فولاد سازی، انرژی به طور غیر مستقیم برای حفر معادن، آماده سازی و انتقال مواد خام شامل زغال سنگ، آھن خام، قراضه و سنگ آھک نیز مصرف می شود. (تقریبا ۸ درصد از کل چرخه حیات انرژی جھت تولید فولاد مورد نیاز است) به طور میانگین ۹۵ درصد از انرژی ورودی ماشین آلات از سوخت جامد (عمدتا زغال سنگ)۳ تا ۴ درصد از سوخت گازی و یک تا ۲ درصد از طریق سوخت مایع تامین میشود.
برای تولید هر تن فولاد نیازمند ۲۰۰ دلار سرمایهگذاری هستیم اما برای تولید هر تن آهن اسفنجی تنها به ۸۰ دلار و برای تولید هر تن کنسانتره و گندله آهن فقط به ۳۵ دلار سرمایهگذاری نیاز است؛ بنابراین عمده سودآوری در نیمه اول زنجیره تولید فولاد است.
بررسی روند میزان تولید فولاد در سطح جهان
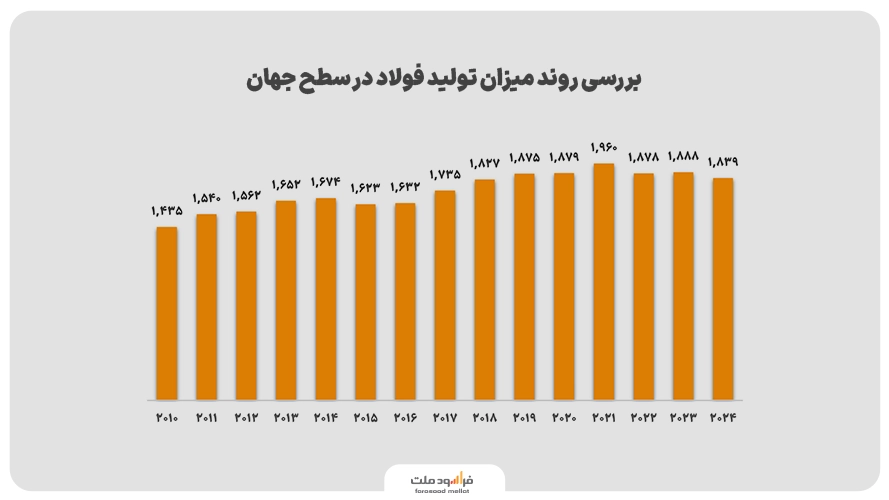
همانطور که مشاهده میکنید میزان تولید فولاد در سال ۲۰۱۰ حدود ۱۴۳۵ میلیون تن بوده و با افزایش۲۹ درصدی به حدود ۱۸۳۹ میلیون تن در سال ۲۰۲۴ رسیدهاست.
بررسی روند میزان تولید فولاد در ایران
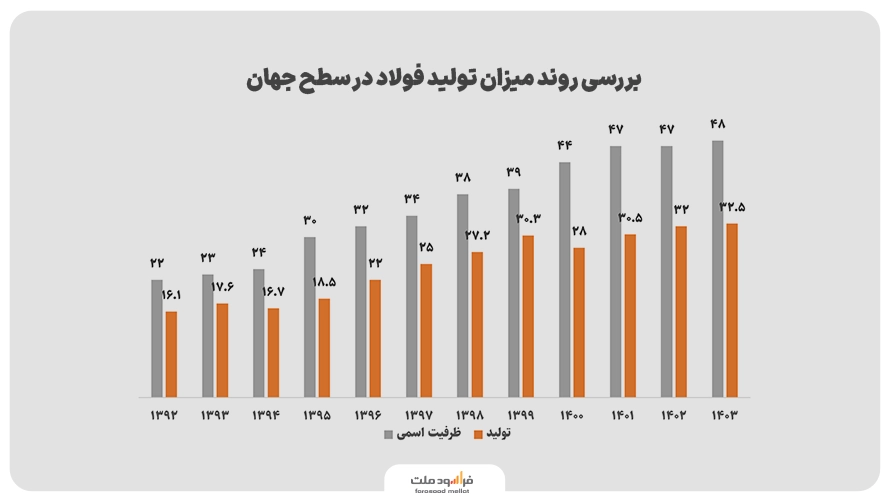
همانطور که مشاهده میکنید ظرفیت اسمی فولاد در ایران با رشد بیش از ۱۰۰ درصدی به ۴۸ میلیون تن در سال ۱۴۰۳ رسیده است، همچنین ایران با تولید بیش از ۳۲ میلیون تن فولاد در سال دهمین کشور تولیدکننده فولاد در سطح جهان است.
روند حاشیه سود ناخالص صنعت فولاد
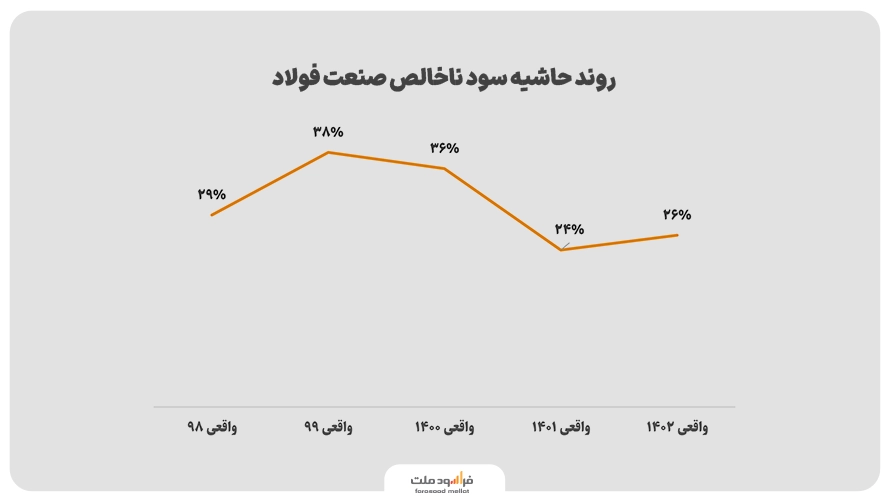
در نمودار بالا روند حاشیه سود ناخالص صنعت فولاد در ایران را مشاهده میکنید. طی سال های ۹۹ و ۱۴۰۰ با توجه به سیاستهای انبساطی بانک های مرکزی کشورهای مختلف و رشد قیمت های جهانی، حاشیه سود شرکت های فولادی رشد قابل توجهی داشت. به مرور با توجه به افزایش تورم و به کارگیری سیاستهای انقباضی و افت قیمت های جهانی و افزایش فاصله دلار ازاد و دلار نیمایی و محدودیت های انرژی ،حاشیه سود شرکت های فولادی با افت مواجه شده و پیشبینی میشود این روند ادامه داشته باشد.
بررسی روندتاثیر صنعت فولاد در تولید ناخالص ایران
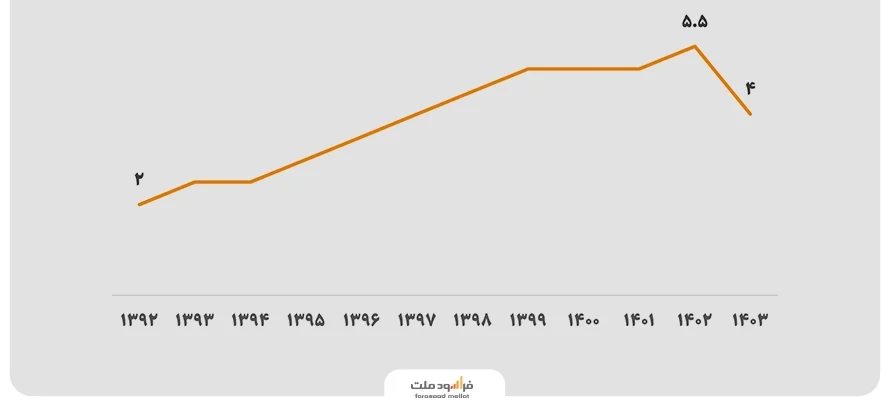
در نمودار بالا روند تاثیر صنعت فولاد در تولید ناخالص داخلی ایران مشاهده میکنید.
این عدد در سال ۱۳۹۲ حدود ۲ درصد بوده و باتوجه افزایش ظرفیت تولید در سال ۱۴۰۲ به حدود ۵.۵ درصد رسیدهاست.